|
The gating system is one of the most important issues with custom injection molding. The gating system is a complete transport channel that guides the plastic melt from the injection machine nozzle to the mold cavity. It has the functions of mass transfer, pressure holding and heat transfer. It has a decisive influence on the quality of plastic parts. Whether its design is reasonable, affects the overall structure of the mold and the ease of its operation.
The role of the gating system in custom injection molding is to smoothly fill the plastic melt into the depth of the cavity to obtain a plastic product with a clear outline and excellent internal quality. Therefore, in the filling process, it is required to be fast and orderly, the pressure loss is small, the heat loss is small, the exhausting condition is good, and the pouring system is easy to separate or cut from the product.
Ordinary runner systems, also known as sprue systems, or gating systems, are the necessary passages for molten plastic from the injector nozzle to the cavity. The runner system includes a main runner, a runner, a gate, and the like.
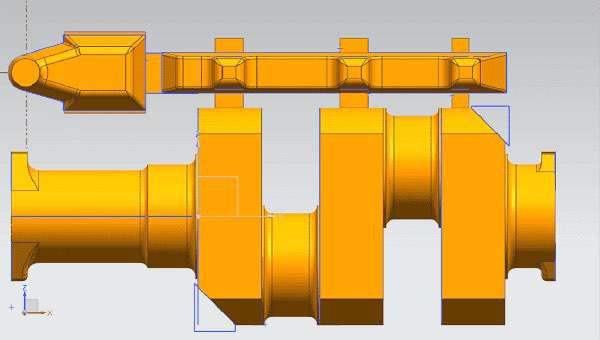
1. Mainstream road
The main channel is a section of the channel connecting the nozzle of the machine to the entrance of the branching channel, which is the first place where plastic enters the cavity of the mold. It can be understood as a flow passage of molten plastic starting from the nozzle of the injection molding machine to the bypass.
2. Shunt runner
Also known as a split runner or a secondary runner. It means a section of the flow path between the end of the main flow path and the gate in the injection or transfer molding multi-cavity or multi-gate mold. With the mold design, it can be further divided into a first split runner and a second split runner.
3. Gate
Also known as the feed port, it is the narrow port between the splitter and the cavity, and it is also the shortest and thinest part. Its function is to use the tightening flow surface to accelerate the plastic, and the high shear rate can make the plastic flow good (because of the shear thinning characteristics of the plastic); the heating effect of the viscous heating also increases the temperature of the material and lowers the viscosity. effect.
4. Cold well
Also known as cold pockets. The goal is to store the cold plastic wave front in the initial stage of the fill filling, preventing the cold material from directly entering the cavity, affecting the filling quality or blocking the gate. The purpose is to store the cold material flowing from the cold head and the melt flowing in the two injection molding intervals to prevent the melt cold material from entering the cavity, resulting in the flow of the next molded product. The location of the cold well is generally set at the end of the main flow channel, but when the length of the split runner is relatively long, a cold well should be placed at the end.
If you need custom injection molding, please contact us.
|
|